Canola seed placed at a consistent depth across the width of the seeding tool will improve seed-to-soil contact, increase seed survival and help the crop emerge evenly. The goal is to have each canola seed placed into the soil at a depth close to one inch.
Seeds placed within the top half inch of soil may have a fairly low rate of survival under dry conditions and seeds below 1.5” depth may have less seedling vigour and lower emergence percentages. The bottom line is that consistent seed placement at around one inch will improve overall canola seed survival across a range of conditions and produce a more uniform stand.
As a result, farmers may want to take time now for a pre-season inspection to make sure their seeding tool can place canola seed at a uniform depth.
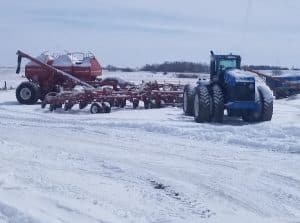
For drills with independently-mounted opener units, check that opener tips are in good shape, packer wheels are properly inflated, depth settings are the same for each unit, all tires are properly inflated and frame height is in line with specifications in the operator’s manual.
For drills with openers on a fixed frame, front-to-back and side-to-side leveling of the frame is key. Tire pressure, hydraulic cylinder seepage, inner-wing down pressure, bent shanks, worn discs and inconsistencies in opener wear are also important inspection points. With these drills, farmers can put them on a flat area, like a concrete pad, to do a pre-season assessment. Lower the openers to about one inch above the ground then inspect each opener to see if they’re in line with the others. Make adjustments as recommended in the owner’s manual. Note that each drill model has different procedures for leveling, even for different models from the same manufacturer.
Repeat these inspections again in the field to assess uniformity under load and with tires on soil.
With field checks, inspect adjacent rows from front, mid, and rear openers and repeat for the centre section and for each wing. Check more frequently at the start of seeding, then monitor as the season continues to check for significant but not otherwise noticeable maintenance issues that can occur throughout the season.
The complete pre-season drill inspection
A good first step is to check with the seeding tool manufacturer for specific adjustments and seasonal maintenance requirements. Most of these details are included in the owner’s manual.
In addition to leveling the drill, as described above, here are other important steps in the pre-season checklist:
Check all openers for excessive wear. Some openers may wear faster than others, especially those that follow tractor or implement wheel tracks. Ask opener manufacturers how much wear is allowable before seed and fertilizer placement is compromised or before plugging is likely in heavier-textured soils. Change openers that exceed this level of wear.
Check tire air pressure and tire size circumference. Tire circumference can differ by 4-8% on the same size tire. Calibrations should accurately simulate the speed of travel, give or take roughly one km/h (or half a mile per hour) as higher speeds require higher rates of product flow per unit time and there may be limitations to the system at higher speeds.
Check that mud scraper gaps are consistent. Mud buildup on tires and packers can lift the whole drill out of the ground, and if mud-pack is inconsistent, it can throw off all other leveling efforts. Make sure mud scrapers on tires, disc wheels and packers have the same gap settings.
Look for excess wear on bushings at pivot points. Worn bushings can cause wings to sag, reducing the consistency of seed depth across the width of the seeding tool.
Check all bearings on rollers and auger delivery systems for possible damage. The seed coating on canola can sometimes leave a residue that can penetrate sealed bearings and may cause drag and bearing wear. Bearing wear can lead to slow or inconsistent rotation of the seed delivering system, causing inaccurate or variable seeding rates.
Check auger flighting and/or fluted roller delivery systems. Look for wear and possible build-up of seed coatings, which can affect accuracy of seed delivery rates.
After running the air delivery system, check at the end of each seed boot for seed and fertilizer. If you have enough plastic cups, put one at the end of each opener. Weigh the contents of each if you want a precise comparison. If amounts are uneven, check metering system components and manifolds for wear or blockages. This is also a good time to check the seed for any cracking due to obstructions or too high a fan speed.
Evaluate air stream flow as it relates to fan speed. To do this, take the hose off the last opener on the outside wing and tie the hose to the frame. Check the air tank manual or with the manufacturer for correct procedures for your drill and tank system. Power up the air delivery system to operating RPMs. If seed and fertilizer are propelled less than 30 cm (12″) or more than 60 cm (24″) from the end of the tube, adjust fan speed or air dampers at the fan outlet to keep seed and fertilizer output within this range. This will reduce seed bounce, damaged seed or plugging at the seed boot outlet.
Check air tank seals to make sure they’re still flexible and provide a complete seal. Don’t leave air tank lids compressed over winter as this may damage the seals.
Do a closer inspection for air leaks. Apply a mix of water and dishwashing soap around hose connections, manifolds, metering systems and air tank seals. Bubbling of the mixture indicates an air leak. Tighten or readjust seals to stop the leak. Air leaks can lead to reduced pressurization or reduced air flow in parts of the delivery system, which can reduce the accuracy of seed and fertilizer rate and placement.
Give all product delivery hoses a quarter turn to reduce wear spots. This will also reduce drag within the hose, which helps maintain accurate seed delivery rates. Check for cracks and spots where hoses are worn through. Replace hoses that are damaged.
Check seed monitor sensors. Buildup of seed coatings on monitor sensors can affect accuracy. Also, make sure the number of pulses per kilometre (mile) is set properly. Note that tire size, tire pressure and soil conditions can influence sensor performance.
Once seeding starts, farmers are encouraged to do in-field inspections to double-check the depth settings. Operating under load may change operating depth, especially front to back. In-field inspections will also show how much soil is thrown over the front-row openers. Slowing down can reduce these effects.
Dig deeper:
- For more on how to do an in-field depth check, see the Equipment Management chapter in the the Plant Establishment section at canolaencyclopedia.ca.
- Watch a Canola School video with Shawn Senko.
- Listen to a new Canola Watch podcast on this topic.